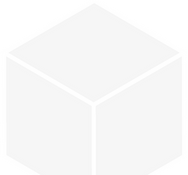

Aufgrund unseren praxisorientierten Prozesserfahrungen aus der Industrie können wir auf erfolgreich umgesetzte Implementierungsprojekte bei mittelständischen Kunden und bei Großunternehmen zurückblicken. Die Prozess Simulation umfasst die Unterstützung des gesamten Produktlebenszyklus mit modernsten Informationstechnologien. Dabei führen innovative Lösungen im Bereich 3D-Visualisierung, Simulation einzelner Prozess-Schritte, virtuelle Produktentwicklung und Konkurrent Engineering zu Qualitätsverbesserungen, markanten Durchlaufzeitverkürzungen und zu Produktkostensenkungen.
Wir definieren gemeinsam mit unseren Kunden ein Projekt, in dem der Fokus auf die Erstellung einer virtuellen Prozesslandkarte der Produktfertigung und deren Einbettung in einer „Digitalen Fabrik“. Das Ziel ist es, eine Ressourcen- und Investitionsplanung innerhalb der Prozessplanung von Produkt-Herstellung aufzubauen. Um das Ziel zu erreichen, werden folgende Themen behandelt:


MODUL I: ERSTELLUNG VON PROZESSKARTEN
Die Prozesslandkarte dient zunächst dazu, alle notwendigen operativen Tätigkeitsfolgen zu systematisieren und vor dem Hintergrund eines Routinebetriebes hinsichtlich organisatorischer Aufbau- und Ablaufstrukturen qualitativ zu beschreiben. Ausgehend von diesem gerne zunächst als „kommunikatives Modell“ zu bezeichnenden Ansatz werden die Grundlagen gelegt um später quantitative Aussagen über Kosten, Zeiten, Qualitäten und Personaleinsatz treffen zu können.
-
Geschäftsprozesse erstellen (Hauptprozesse, Arbeitsschritte, Elementartätigkeiten)
-
Reportkonzept erstellen hinsichtlich Parametrisierung und Fragenbeschreibung
-
Workshops organisieren, durchführen, auswerten

MODUL II: PARAMETRISIERUNG DER PROZESSKARTEN
Nachdem nun alle relevanten Fragestellungen bestimmt sind, erfolgt auf Basis von Modul-I eine durchgängige operative Parametrisierung der Prozesslandkarte: Beispielsweise werden Attribute wie „durchschnittliche Bearbeitungszeit“, „maximale Fräsdauer“ oder „Häufigkeit des Lackierprozesses pro Monat“ als relevante Größe definiert und als Grundlage einer qualitativen Auswertung des Prozessmodells vorgesehen. Die dabei gewonnen realen Daten werden für die einzelnen Tätigkeiten innerhalb der Prozesslandkarte als Grundlage algorithmischer Berechnungen hinterlegt.
-
Anpassung der Attributisierung auf Basis des Reportkonzeptes
-
Workshops zur Parametererhebung (Feinkonzept, Parametrisierung)
-
Prozesskarte füllen mit aufgenommenen Parametern
-
Vorarbeit zur Reportumsetzung

MODUL III: HINTERLEGUNG DER FERTIGUNGSMASCHINEN
Es wird hier unter „Fertigungsmaschinen“ den Parameterset verstanden, der sich durch die Einstellung und Handhabung der Maschinen ergibt. Solche Parameter haben einen großen Einfluss auf die Performance und Robustheit des finalen Produktes. Deshalb ist die Erfassung dieser Parameter und deren funktionalen Zusammenhang sehr entscheidend. Unser breit angelegtes technisches Fachwissen in vielen Industriebereichen ermöglicht uns, durch den Einsatz von modernen Methoden der mathematischen Optimierung eine optimale Lösung zu finden. Im Allgemeinen handelt es sich z.B. um konstruktions-/werkstofftechnische Parameter, Randbedingung und Handhabung.
-
Hinterlegung der Maschinen in die Prozesslandkarte
-
Definition der Designparameter in die Prozesslandkarte basierend auf die durchzuführenden Workshops
-
Designparameter in die Prozesslandkarte zu Maschinen hinterlegen
-
Reportkonzepte Umsetzung

MODUL IV: DIGITALE FABRIK
Das Internet der Dinge hat die Grundlagen für eine vernetzte Fabrik geschaffen. Das Konzept dieser Industrie 4.0 ist einfach: in den verschiedensten Geräten werden kleine Datenspeicher verbaut, die per Funk ausgelesen und beschrieben werden können. Über das Internet oder ein anderes Netzwerk können diese Daten miteinander verknüpft und weiterverarbeitet werden. Wendet man diese Technik nun auf die Maschinen und Geräte einer Fabrik an, entsteht ein sogenanntes „cyber-physical system“ (CPS), also eine Infrastruktur, in der die einzelnen Maschinen des Produktionsprozesses selbstständig miteinander kommunizieren können.